- AddressNo.188 East Changjiang Road, New District, Wuxi, Jiangsu,China
- Factory AddressNo.188 East Changjiang Road, New District, Wuxi, Jiangsu,China
- Worktime86-510-85310188
- Phone(Working Time)86-510-85310186
- Phone(Nonworking Time)86-510-85310189
- Fax86-510-85310187
Quality Control
|
| Yes | No | NA |
1. | Have quality targets and quality policy been formulated by the company management and is this known to all employees? |
|
| √ |
2. | Is there an independent system control in the company and has a responsible person been named by company’s management for system management? |
√ |
|
|
3. | Is a management system described in a manual? | √ |
|
|
4. | Are internal audits carried out to support the continuous improvement of the processes? | √ |
|
|
5. | Are statistical method used to measure the process capability? | √ |
|
|
6. | Are contract, ordering and amendment details checked for completeness and feasibility prior to submitting the offer? | √ |
|
|
7. | Is there assurance that the distribution documents (drawings, delivery specification) are correctly controlled, in order to prevent the unintentional use of obsolete document? | √ |
|
|
8. | Is there a system with which the identification and traceability of the materials and the product is ensured in all phases of the production process? |
|
| √ |
9. | Are the workflows in production / order processing planned and documented? Status checked for adherence to delivery schedules? | √ |
|
|
10. | Are inspection and work instruction available for employees, as well as visualizations, if applicable? | √ |
|
|
11. | Are the employees trained for their respective work processes and suitably qualified – are training courses planned, carried out and documented? | √ |
|
|
12. | Is there assurance for products that do not conform are removed from the production flow or warehouse and not reach the customer? | √ |
|
|
13. | Is the goods inspection carried out with critical parameters included in checklist? | √ |
|
|
14. | Is a process used for the analysis of causes of errors in order to avoid repeated errors and initiate targeted corrective and preventive measures? | √ |
|
|
15. | Are production and testing facilities regularly maintained after documented planning? |
|
| √ |
16. | Is all measurement and inspection equipment calibrated according to defined intervals and the results documented? | √ |
|
|
17. | Is the calibration status identifiable for the employees who use the measurement and inspection equipment? | √ |
|
|
18. | Is the out-of-calibration measurement and inspection equipment isolated from unintended usage? | √ |
|
|
19. | Are possible sub-contractors that deliver materials or services qualified with respect to fulfilling the customer requirements? |
|
| √ |
20. | Is there a list of approved suppliers, whose quality data are assessed at least 1x per year? | √ |
|
|
21. | Are goods inspection carried out on delivered products? | √ |
|
|
22. | Is the return processing organized (8D Report)? |
|
| √ √ |
23. | Are customers (e.g. ERIKS) immediately informed about delivery date delays or other non-conformities? | √ |
|
|
24. | Are controls established to ensure packing methods/specifications confirm to requirement? | √ |
|
|
25. | Is the customer satisfaction documented? | √ |
|
|
Certifications
Oil-Field Bearing Industrial Co.Ltd main supply the SKF,FAG,INA,TIMKEN,NSK,NTN bearings to the world.
If you have any inquiries,please send me inquiry at Contact US page.
The following is our comprehensive range:
1.Deep groove ball bearings:600,6000,6200,6300,6400,1200,1300,16000,6000 in open,Z,RS,ZZ and 2RS series.
2.Bearing units:UC,UCP.UCF,UCFL,UCPA,UCFC,SA series.
3.Matric and Inch size Tapered roller bearings:30200,32200,30300,32300,31300,32900,32000,33000,33100,33200 series.
4.Spherical roller bearings:222,213,230,231,240,241 series.
5.Needle roller bearings:NK,NKS.NA,RNA,HK,BK,etc.
6.Cylindrical roller bearings:N,NU,NUP,NJ,RN,RNU,etc.
In addition, we not only supply bearing,but also sell:oil seals, washer, lubricator, bearing ball, hydraulic pump and accessories.
Expect to cooperate with you in near future~
Contact Us
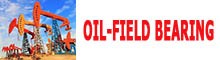
- Oil-Field Bearing Industrial Co.Ltd
- AddressNo.188 East Changjiang Road, New District, Wuxi, Jiangsu,China
- Phone(Working Time)86-510-85310186
- Fax86-510-85310187